
Lawyers for Industrial Accident Victims
Lawyers for Industrial Accident Victims
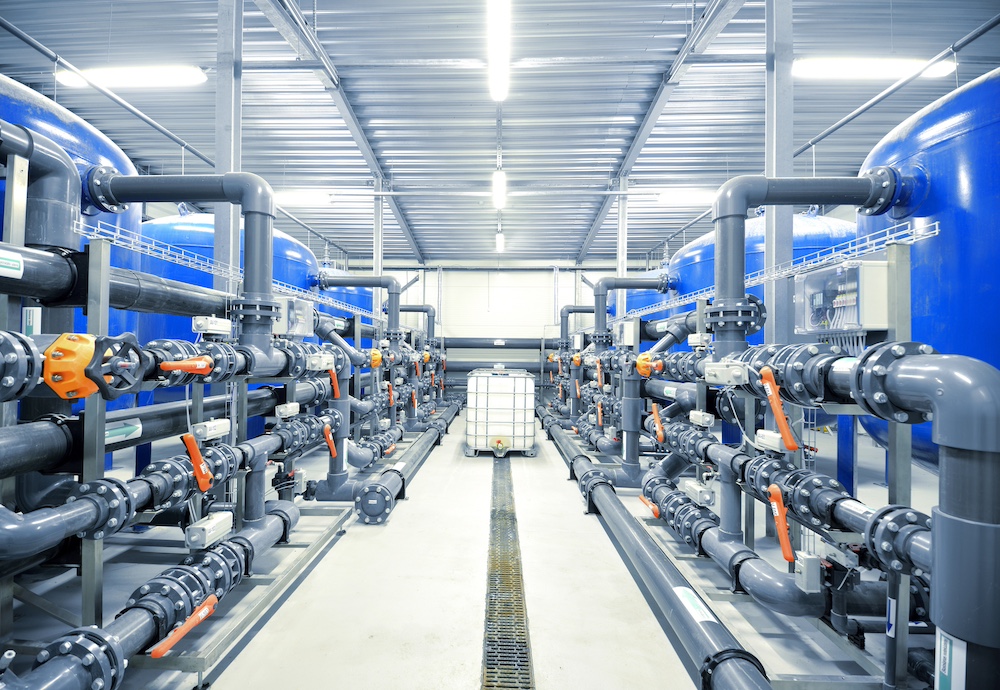
Common Types of Industrial Accidents
Free Legal Consultations
If you or someone you know has been injured in a motor vehicle accident, alert Lead Attorney Doug Horn to the case at 816-795-7500. Horn offers free legal consultations. In addition to telephone consultations, Horn offers office, home, and hospital consultations to provide aid to clients at a convenient location.
As rapid response attorneys, early legal consultation is a priority with Horn Law. An early start allows us to take care of our clients’ immediate issues, including legal, investigative, insurance, and financial questions that arise in nearly every car accident claim.
Close & Convenient
The Horn Law home office is in Independence, Missouri, near I-70 and I-470 (across the street from Costco).
In addition to our home office, consultation offices are located in both Lee’s Summit and Liberty in Missouri, as well as Overland Park, Kansas.
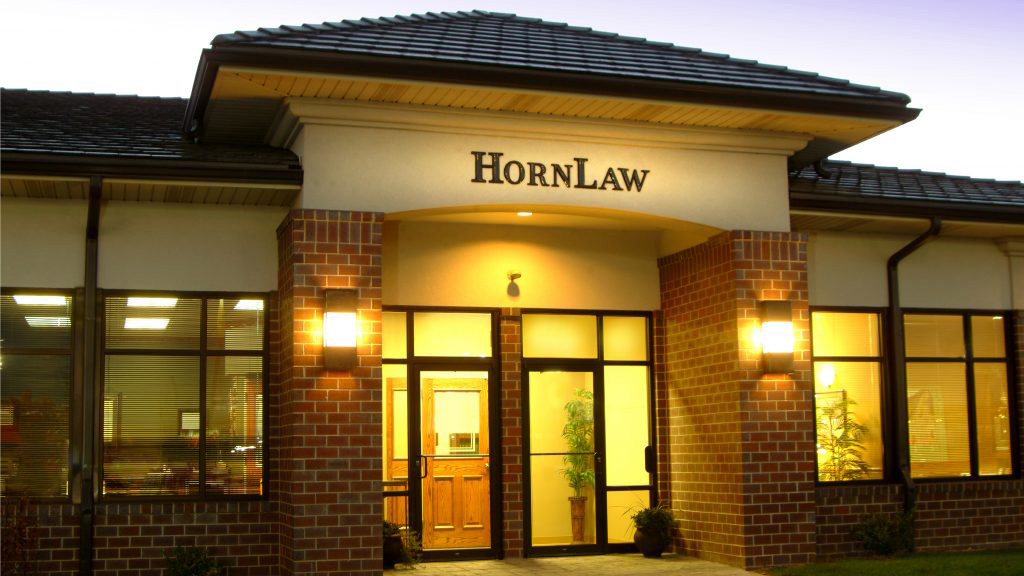
Horn Law At Work
Right from the start, Horn Law will devote our full professional abilities, resources, and experience to obtain a maximum legal recovery. This work is complex, and at a minimum, requires securing important evidence, litigation, and advanced settlement negotiations. Below are our areas of concentration with respect to industrial accident cases. Falls: Falls are the most common industrial accident and the most common cause of death and injury among industrial and factory workers. While safety measures such as hard hats have reduced the damaging effects of falling in some cases, there is still a great danger posed to workers who are completing tasks at high elevations or on slick surfaces. Because of the heights involved in many falls, workers do not just face the risk of severe injury, but also face the risk of death. Potential liabilities include:
- Failure to provide proper equipment, including safety equipment
- Failure to provide appropriate training and supervision
- Failure to accurately assess risks
- Failure to maintain lifts and other elevated surfaces
- Failure to remedy potentially dangerous conditions
- Failure to maintain guards
- Failure to update defective guards or outdated technology
- Failure to provide appropriate training
- Failure to warn inspectors or maintenance crew of risk
- Failure to lock out the machine when not in use
- Failure to provide protective equipment
Toxic Chemical Exposure: Toxic chemical exposure is one of the leading causes of severe injury and death amongst industrial workers because it is not easy to spot until it is too late. Chemicals like ammonia, chlorine, and sulfur dioxide are highly dangerous yet can be a part of the outcome of the production process for many factories. Modern technology has made these and other chemicals much easier to monitor, yet they still pose a significant risk to those working around them. Chemical and drug manufacturing, metal fabrication, and petroleum processing make up more than 90% of all industrial waste in the United States and are highly-regulated processes. However, the guidelines and regulations set forth for the handling of these dangerous substances are not always followed correctly. Potential liabilities include:
- Failure to properly and compressively assess chemical risk
- Failure to provide proper fumigation and output systems
- Failure to train employees to identify any signs or symptoms of chemical exposure
- Failure to provide personal protective equipment
- Failure to maintain, inspect, and review operations protocol
- Failure to remain updated on any new regulations or developments on chemical exposure
- Failure to appropriately train operators
- Failure to update and repair trucks
- Failure to provide specific truck safety training
- Failure to abide by weight/capacity regulations
- Failure to use a vehicle for intended purposes
- Failure to appropriately train electrical operators
- Failure to provide a safe working environment for electricity
- Failure to identify unique risks to wires, etc.
- Failure to utilize correct lockout/tagout protocol.
- Failure to repair or maintain wires, panels, and switches
- Failure to comply with voltage or energy regulations
- Failure to provide training on a uniform lockout/tagout process
- Failure to sufficiently inform employees of lockout importance
- Failure to warn any repairmen or inspectors of any dangers
- Failure to identify and alert managers of any machine issues related to lockout/tagout
Confined Spaces: Small, enclosed areas inherently represent a threat to the safety of industrial workers. In particular, such spaces can furnish very low levels of available oxygen, which can lead to suffocation. Because some of these tank-like spaces may also not provide any visual on a worker, it is necessary to follow and abide by a strict safety protocol thoroughly. If a worker is without oxygen for longer than a few seconds, asphyxiation and unconsciousness can pose a severe and even deadly risk. Further, such states also produce severe injury from falling, especially when working around hard metal and aluminum materials. Potential liabilities include:
- Failure to identify confined spaces and assess their risk
- Failure to train employees on confined space procedures
- Failure to alert inspectors/maintenance personnel that space is confined
- Failure to implement a uniform, consistent emergency protocol for confined space risks
- Failure to identify fire risks and hazards
- Failure to have an action plan for fire emergencies
- Failure to provide upkeep to fire evacuation routes, signage, etc.
- Failure to train employees properly
- Failure to safely dispose of hazardous materials or secure gasoline tanks